Project Overview
Facility: Macy’s Warehouse Reroof
Owner: Macy’s, Inc.
Services: Siplast Lightweight Insulating Concrete (LWIC) Roof Deck system
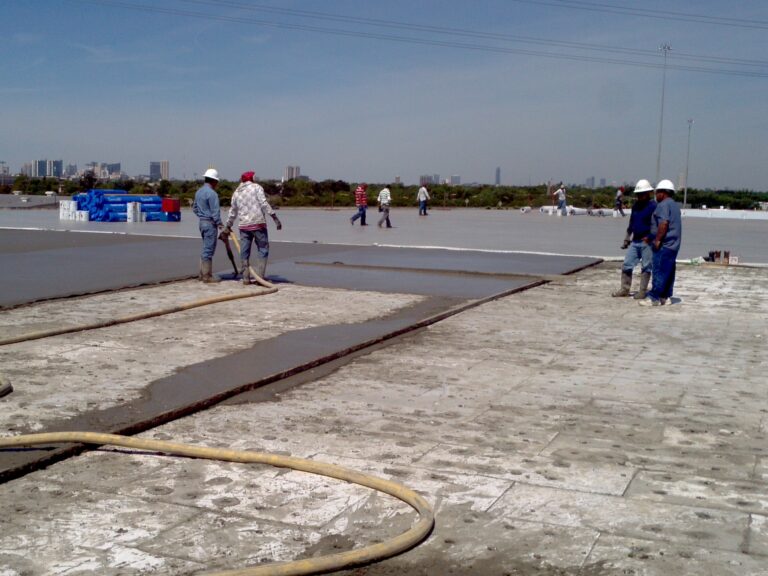
Project Summary
Nettles worked with the roofing contractor to to reroof two large distribution warehouses (243,000 square feet and 346,000 square feet) for Macys. The Lightweight Insulating Concrete (LWIC) roof deck installed by Nettles provided a long lasting roofing solution with a low TCO (total cost of ownership), eliminated the ponding issues with the existing roof, and allowed the roofer to free up their resources while maintaining their project profitability.

The Problem
When Macy’s needed to reroof their distribution warehouses, they wanted a solution that was cost-effective, had a low TCO (total cost of ownership), and was environmentally friendly. The existing roof deck had significant drainage issues that resulted in ponding water in several areas. In order to deal with the ponding issues, both buildings needed to have a positive drainage to a gutter system over very long runs. In addition, owners planned on occupying the facilities for over 20 years so it was important for them to get a roof deck system that would last and have a low cost when it came time to reroof the buildings.
By understanding the key advantages of LWIC, the roofing contractor was able to employ Nettles as a subcontractor. This allowed the roofing contractor to oversee the taper system, maintain his project profitability, and save the owner money.

The Nettles Solution
Nettles and the roofing contractor determined that the best solution for the owner was to reroof both facilities with a Lightweight Insulated Concrete roof deck (LWIC). The LWIC roof deck provided several significant advantages over traditional roofing solutions:
- Eliminate Ponding and Provide Excellent Insulation: Using the LWIC roof deck, Nettles was able to correct the issues with ponding water and provide positive slope to the gutters at 1/16” due to the extremely large runs. Our insulation in the roof system reached thicknesses of over 21” at some of the high points which provided excellent insulation as well as the required drainage.
- The LWIC approach for the tapered system saved owner and roofing contractor TIME and MONEY: The size of the project, budget and the quick turnaround required by the owner made LWIC the ideal solution. Nettles was able to pour the LWIC roof deck at over 8,000sf per day and was available for the roofer to install their membrane within a 48-72 hour window.
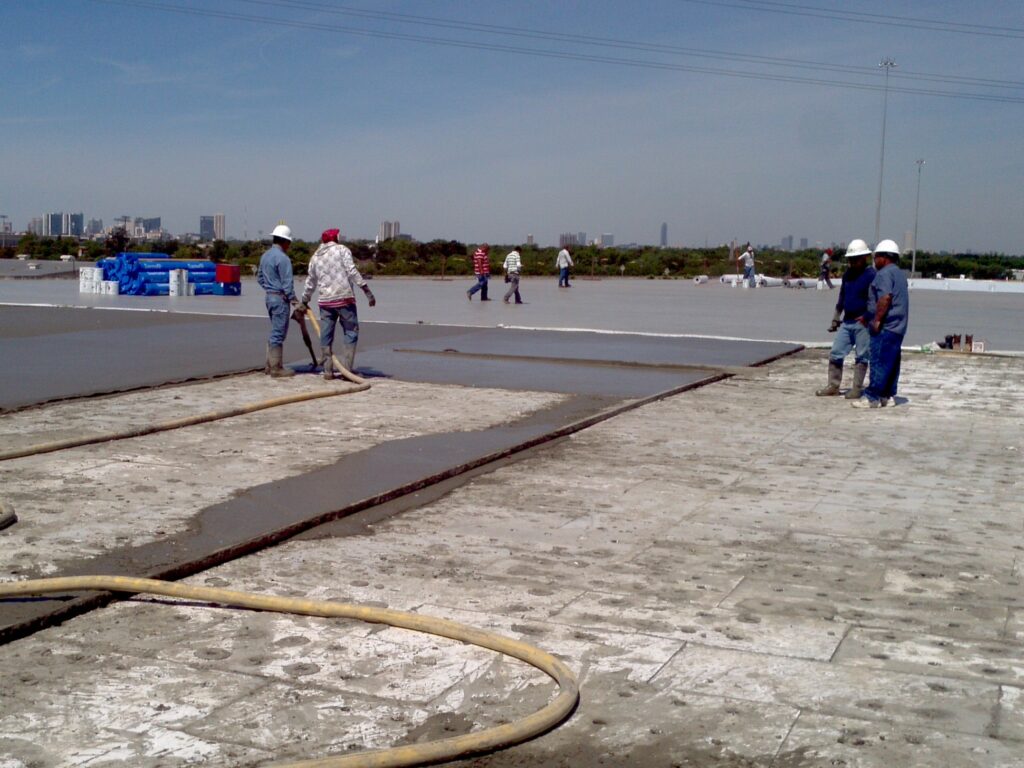
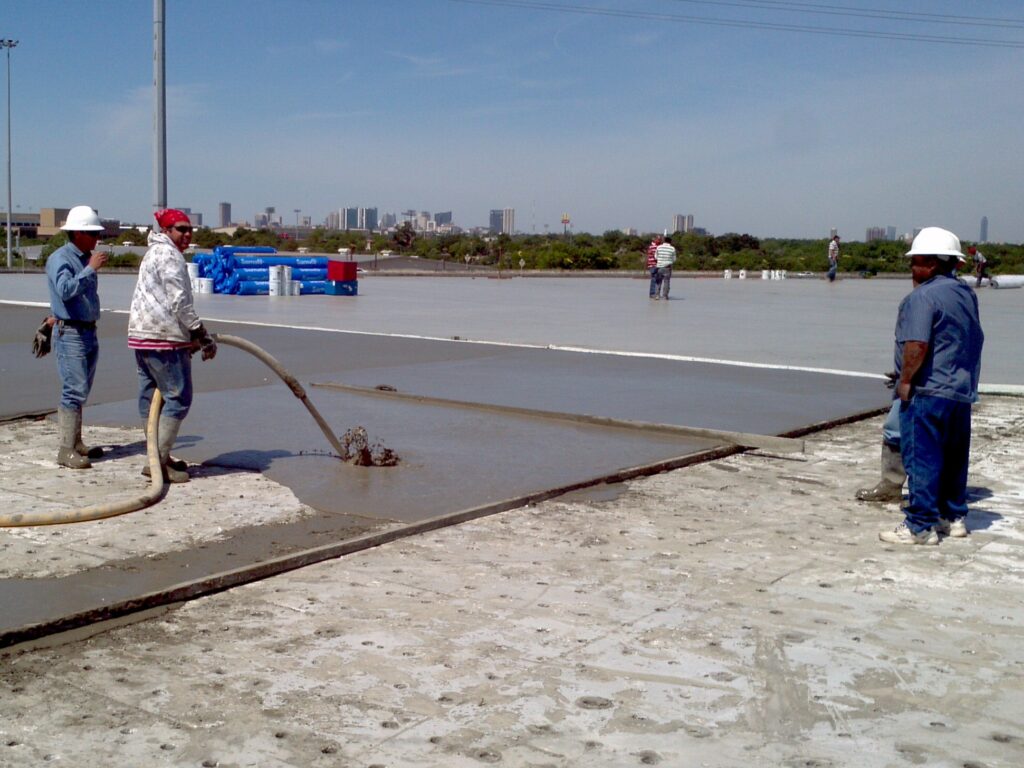
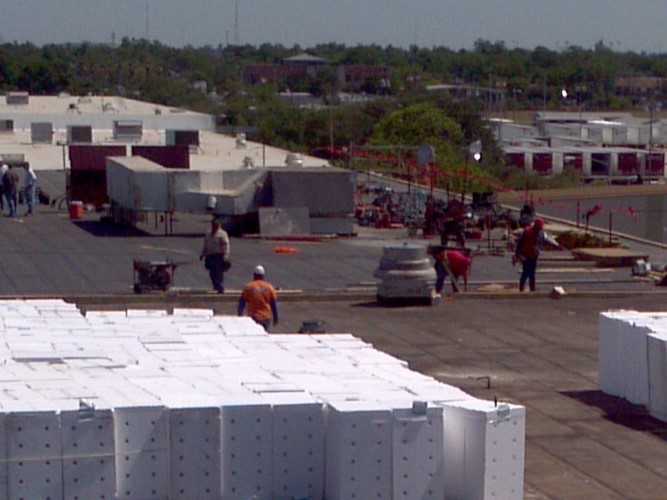
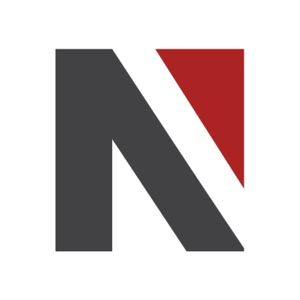
Reroofing With A Taper Lwic Roof Deck System Is The Best Choice For Both The Owner And Roofing Contractor.
The owner benefits from a longer lasting roof deck system; less thermal shock on the new roof membrane (longer lasting roof); a lower lifetime cost system
The roofing contractor benefits by having the ability to free up company manpower and maintain profitability with a trusted subcontractor.
If you are looking for the best solution for your next reroofing project, contact Nettles and we can discuss the economics of using LWIC for reroofing and how it makes sense for the owner, architect, general contractor, and roofer.